工程管理及び改善の進め方
工程管理とは
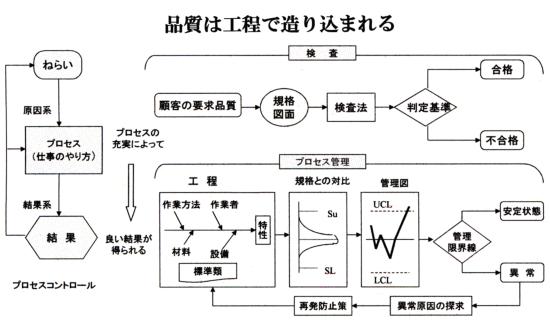
工程管理の目的
工程管理は、制御可能な
1.人(Man):教育・訓練
2.設備(Macine):設備総合効率
3.材料(Material):基準・バラツキ
4.方法(Method):管理標準
5.環境:作業・インフラ
現場にはこの4Mプラス環境を経済的に管理し、Q(品質)C(原価)D(納期)の向上を図る
工程管理7つの手順
1.品質標準(管理工程図)を決める
2.品質を達成する為の作業手順を決める
3.作業者の教育訓練を行う
4.作業を実施する
5.作業が指示通りに行われているかチックする
6.異常に対し処置をとる
7.処置の効果を確認する
品質改善の進め方
TQC(総合的品質管理)活動 1.組織作り→2.品質の定義→3.幹部教育→ 4.ポリシー宣言→5.QC教育→ 6.実践→7.診断→8.反省・是正・歯止め *1-8のPDCAを回しながら推進する |
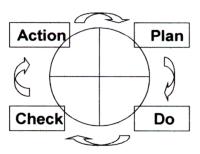 |
改善テーマ
・目標のQ:品質問題をゼロにする
・目標のC:圧倒的優位の原価力を獲得する
・目標のD:必要な時に必要なものを数だけ流す又は納入 |
*QCDは相互に相関することを踏まえ、その体制をより効率的に築くことが必要 |
管理と改善の違い
|
仕事のやり方 |
望ましい結果 |
仕事の結果 |
管理 |
一定に保つ |
安定 |
不良率が下がる |
改善 |
積極的に仕事のやり方を変える |
不良率が減少 |
不良率が減少 |
*管理(維持)活動の結果は、全体が低くなる
*改善活動の結果は、順位が下がり田の特性は、現状のままあるいは工程が管理されていないと他の項目が逆に高くなる
改善のテーマと計画
・目標のQCDと現状のギャップは、仕事の「悪さ加減」であり、このことを改善テーマとして計画を立案する |
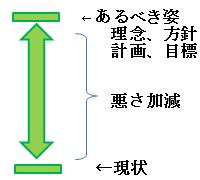 |
・改善ステップは、次の「7つのステップ」の管理サイクルによる |
七つのステップ
1問題の把握 |
何を(What) |
Plan |
管 理 の サ イ ク ル |
2問題の現状分析 |
3要因分析(課題) |
なぜ(Why) |
4対策の立案、実施計画 |
どのように(How When Where Who) |
5対策の実施 |
DO |
6成果の確認 |
Check |
7歯止め |
action |
「工程改善」課題解決のポイント
従来の制約条件、過去の検討結果では問題解決不可能
― 見方を変えて(白紙に戻して)考える
― 他に学ぶ 他を応用する
― 問題の本質を見極める(なぜなぜ分析)
― 問題の中身を克明に定量的(数値で)に調べる
― 根本原因(真の原因)の究明 対策を急がない
― 改善効果のものさし(指標)の事前設定と効果の確認
― 改善内容の標準化と水平展開